Lean + TeamSTEPPS = LeanSTEPPS
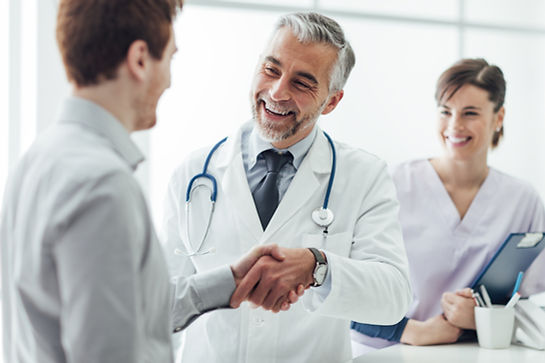
Six Ways You'll Benefit from LifeWings LeanSTEPPS
The "Standard" will be known by all and the Protocols to ensure standards are kept will be known and used by all staff - who will hold each other accountable to use them. Quality of care measures will improve.
You'll end up with an "army of problem solvers" - frontline staff with the skills to conduct process improvement. Costs will go down. Staff engagement will go up. Results will be sustainable.
Staff are trained to provide peer-to-peer accountability and use stop-the-line assertion, cross-check, and mutual support to ensure accountability to use Standard protocols. HAC and wasteful "do-overs" will stop.
Physicians’ and nurses’ communication is interactive, respectful, and collegial. There is a sense of psychological safety that allows for inputs and concerns. Physician and staff satisfaction will improve. Nursing turnover will drop.
Peer-to-peer and team-based performance feedback (debriefing) will become a routine behavior. The organization will get better every day and experience continuous quality improvement.
Hardwiring of effective communication between care givers will become the norm, leading to fewer errors, & near misses, and less patient harm or HACs.
How It Works
LifeWings blends all of the elements of TeamSTEPPS plus Toyota Lean process improvement into one united effort‐‐ one that provides administrator, physician, and nursing engagement and support of standardized work at the outset, and sustained results over time.
We build an operationally enhanced patient experience by using Lean to create standard practices for improved on‐time starts, optimized patient flow, and patient and procedure room readiness. We also create fully balanced staffing, scheduling, and surgical or procedure block times. Result? Quality, safety, and cost effectiveness. But, it doesn’t matter how efficient these standardized practices are, if staff don’t, or won’t, use them.
To ensure accountability, LifeWings changes your culture through training to ensure every member of the team can make a stop‐the‐line assertive statement, communicate without error, and collaborate like an expert team.
LeanSTEPPS Results
Case Study #1
$470K Invested Produced $2M in Returns.
-
Improved: OR On‐Time Starts = 100%, a 51% improvement;
-
OR Room Turn Over Time = 23.9 Min, a 35% improvement;
-
OR Anti‐Biotic Timing Compliance = 97% a 1% improvement;
-
DSU Holding Wait Time = 0.0 Min (Eliminated This Step);
-
DSU patient Prep Time = 30.4 Min, a 31% improvement;
-
PAT Phone Interview Time = 29.6 Min , a 27% improvement;
-
Case Readiness 72 Hrs. Out = 28.6%, a 60% improvement.
Case Study #2
$8.5M Invested Produced $30.5M in Returns.
-
Case Study #2
-
Increased Pre‐Op Antibiotic Prophylaxis Timing Compliance > 95%, in all areas, from a low of 60%;
-
Increased OR cases per day capacity while decreasing patient flow time;
-
Increased On Time Starts First Cases to 90%, from 33% previously;
-
Reduced Average Room Turnover Time to 16.1, from approx. 35 Min previously;
-
DSU PT Prep Time 30.4 Min, a 31% improvement.
Case Study #3
$484K Invested Produced $1.5M in Returns.
-
Sentinel events reduced to 1 from average of 6 –7 per year;
-
Serious safety events rate lowered from 5.83 to 0.48;
-
3 year Mortality index lowered from 0.97 to 0.59;
-
Days on ventilator reduced from 240d to 173d;
-
74% of all Safety Culture Survey indicators show improvement;
-
ICU’s reduced RN turnover costs by $187,000 annually;
-
Surgical Services reduced RN turnover costs by $345,000 annually